Why Industrial Facilities Should Develop an In-House Leak Management Plan
May 11, 2023 10:35:09 AM Resources 6 min read
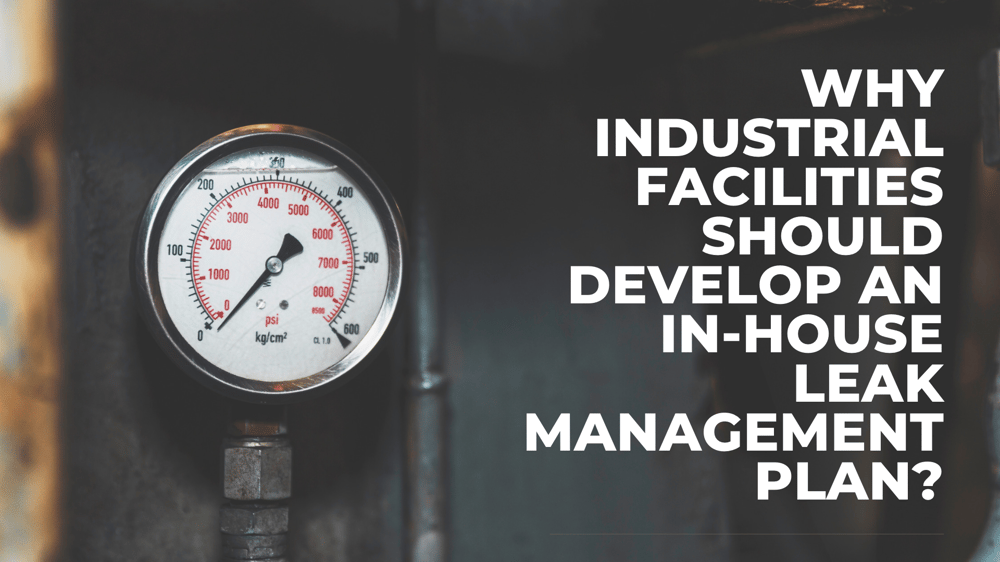
How to use a Smart Tablet
To visually locate leaks at your facility?
Words cannot fully describe all the smart capabilities of the Prosaris OL1, but our live demo certainly can. Experience the exciting action of locating leaks, quantifying and managing leak records in real-time, all through screen share.
Air leaks are a widespread and challenging issue in industrial facilities and a chronic source of compressor performance inefficiency. Leaks lead to significant energy waste (and higher energy bills). Where leaks impact equipment, or component function, they can result in operational interruption, increased system maintenance and have the potential to create safety hazards. Most of the time, air leaks go unnoticed, which means leaks in a noisy facility can be left unchecked for years, resulting in many thousands of dollars of wasted energy. In fact, according to the U.S. Department of Energy, industrial facilities can lose around 20-30% of their compressed air through leaks. For these reasons and more, an in-house air leak management plan is essential for any facility striving for operational efficiency.
To manage a facilities compressed air leak problem, many industrial facilities either hire external consultants to complete their leak audits, train internal staff to use traditional ultrasonic devices, or opt for the more expensive ultrasonic visualizing technology to remove the training requirements of the more traditional tech and empower their personnel to find and repair leaks.
Investing in the training of staff to use more traditional ultrasonic devices can be a risk with the more fluid nature of employee retention these days. As such many companies will invest in external specialist consultants who are often well trained in the use of the traditional devices, and skilled individuals with sound facility and plant knowledge. The reports these consultants issue can provide an enticing view of the savings which could be realized. However, the reality may be that many of those leaks do not provide good return on effort and the end user still needs to manage their internal maintenance resources to plan the return to the location and sourcing of the equipment and parts required for the repair. As these report findings need to be manually moved into a repair management system to plan the work, it is often the case that these reports sit on a shelf and many of the same leaks are found and tagged the following year. For facilities that do look to take on the leak audits themselves, many will opt to purchase the newer visualizing tech in the hope that they will be simple to use. That may not be the case for all and users often find that the investment required to purchase such a device results in the device being shared across multiple facilities. This can cause delays in the leak repair process and post-leak repair verification, and can become costly in the long run.
Regardless of the approach taken to detecting and locating leaks, it is clear that this is just part of the leak lifecycle and without prioritization, assessment of value and planning for, and implementing the repair, the savings and incentives will generally not be fully realized. As such, a compressed air leak management plan is essential and should provide a comprehensive program that aims to minimize compressed air leaks in an industrial facility and maintain a reduced overall leak profile for the facility, year after year. A solid plan will typically involve several steps, including leak detection and identification, tagging, tracking, assessment of repair activity, assignment of action, repair and verification. By implementing an in-house leak management plan, an industrial facility can effectively manage and reduce compressed air leaks, this in turn will minimize its environmental impact and improve the facilities overall energy efficiency.
Cost Savings in Detecting and Fixing Compressed Air Leaks
You may ask yourself, “How much do compressed air leaks cost?”. Although estimating the exact cost of compressed air leaks can be challenging, they do cause tremendous energy waste, resulting in higher energy bills for the facility. If left undetected and unaddressed, air leaks can cost your facility upwards of tens of thousands of dollars annually.
Beyond the obvious saving from reducing the energy consumed trying to overcome the leaks found, developing an in-house air leak management system can also save additional costs through reduced maintenance. A compressed air system that is delivering supply to its designed demand will perform better than a system operating outside of its preferred operational state. Air leaks themselves can create pressure challenges on end use devices, this can result in excessive wear and tear on equipment, leading to breakdowns and repair or replacement. By reducing air leaks, an industrial facility can extend the lifespan of its equipment and reduce the frequency of maintenance and repairs, resulting in even more savings over time.
Environmental Impact of Compressed Air Leaks
Because of the energy wasted by compressing air which is simply lost to leaks, a facilities compressed air system can be a cause of significant negative environmental impact.
According to the US Department of Energy, up to 50% of the compressed air produced by industrial systems is wasted due to a combination of leaks, improper use, and poor maintenance practices (of these three main causes, leaks are by far the most dominant cause). This represents a significant loss of energy and resources, which can have a negative impact on the environment. The energy wasted by compressed air leaks also leads to increased greenhouse gas emissions, which can contribute to climate change. The EPA estimates that every 1,000 cubic feet per minute of compressed air leaks results in the emission of 9,000 tons of carbon dioxide per year.
In some cases, rebates and incentives may be provided by utilities and government to promote efforts that reduce environmental impact. For instance, some utility companies offer rebates or incentives to industrial facilities for implementing energy-efficient measures, such as air leak detection and repair, compressed air system optimization, and more measures aimed at overall reduction of the compressed air systems energy consumption. These rebates and incentives can offset the initial investment in the hiring an external consultant to support with an audit and compressed air system overall optimization, or purchasing equipment solutions for in-house action to locate and repair compressed air leaks.
According to the Database of State Incentives for Renewables & Efficiency, many states offer tax incentives, grants, or loans to encourage energy efficiency in commercial and industrial buildings. By taking advantage of these incentives, industrial facilities can reduce their environmental impact, save money, and improve their bottom line.
Tracking Compressed Air Leaks Over Time
An in-house air leak management plan can be valuable for identifying recurring leaks and tracking progress over time. By periodically monitoring the plant for air leaks and collecting data on where and when they occur, an effective leak lifecycle management system can help identify patterns and trends in leak occurrence. This can move a facilities approach to leak management from reactive to proactive.
For example, suppose the same leak is detected in the same location multiple times. In that case, it may indicate that the initial repair was ineffective or an underlying issue with the equipment or process in that area is the cause of loss (this may be the choice of component used). By identifying these recurring leaks and investigating the root causes, the plant can take corrective actions to prevent them from happening.
Additionally, tracking the progress of air leak management efforts over time can provide valuable data for workforce demand and provide opportunities for continuous improvement. By analyzing trends in leak occurrence and the effectiveness of repair efforts, the plant can identify areas for improvement in its leak detection and repair processes. This can lead to more efficient and effective air leak management, further reducing energy waste and associated costs.
Conclusion
An in-house air leak management plan can improve the efficiency, safety, and environmental impact of an industrial facility while also reducing costs and ensuring compliance with regulations. By investing in an air leak management system, industrial facilities can reap significant benefits for their operations and the environment. Such a plan can contribute to a company's sustainability goals and reputation, attracting more clients and stakeholders.
Prosaris provides a comprehensive solution for industrial facilities seeking to improve their air leak management approach. Our OL Series device, combined with the Prosaris Leak Management app, offers a unique and cost-effective approach to detecting and locating even the smallest leaks. But that's just the beginning - our solution includes the ability to record and analyze leak data, as well as supporting the assessment and prioritization of repairs and the management and recording of leak repair activities (including the leak pre and post repair status to aid utility program compliance). With Prosaris, you can take control of your compressed air leak management and see significant cost savings, improved efficiency, and a deliver a more sustainable operation for your facility.
Our goal is to normalize ultrasonic compressed air leak detection for everyone. Our solution is simple to use, lightweight, accessible and quick to deploy and we support you from the first point of leak identification, right through to resolution and assessment of action value.
Interested in implementing an air leak management system but not sure where to start? Contact us today for expert guidance and advice on how to improve your industrial plant's energy efficiency and sustainability.